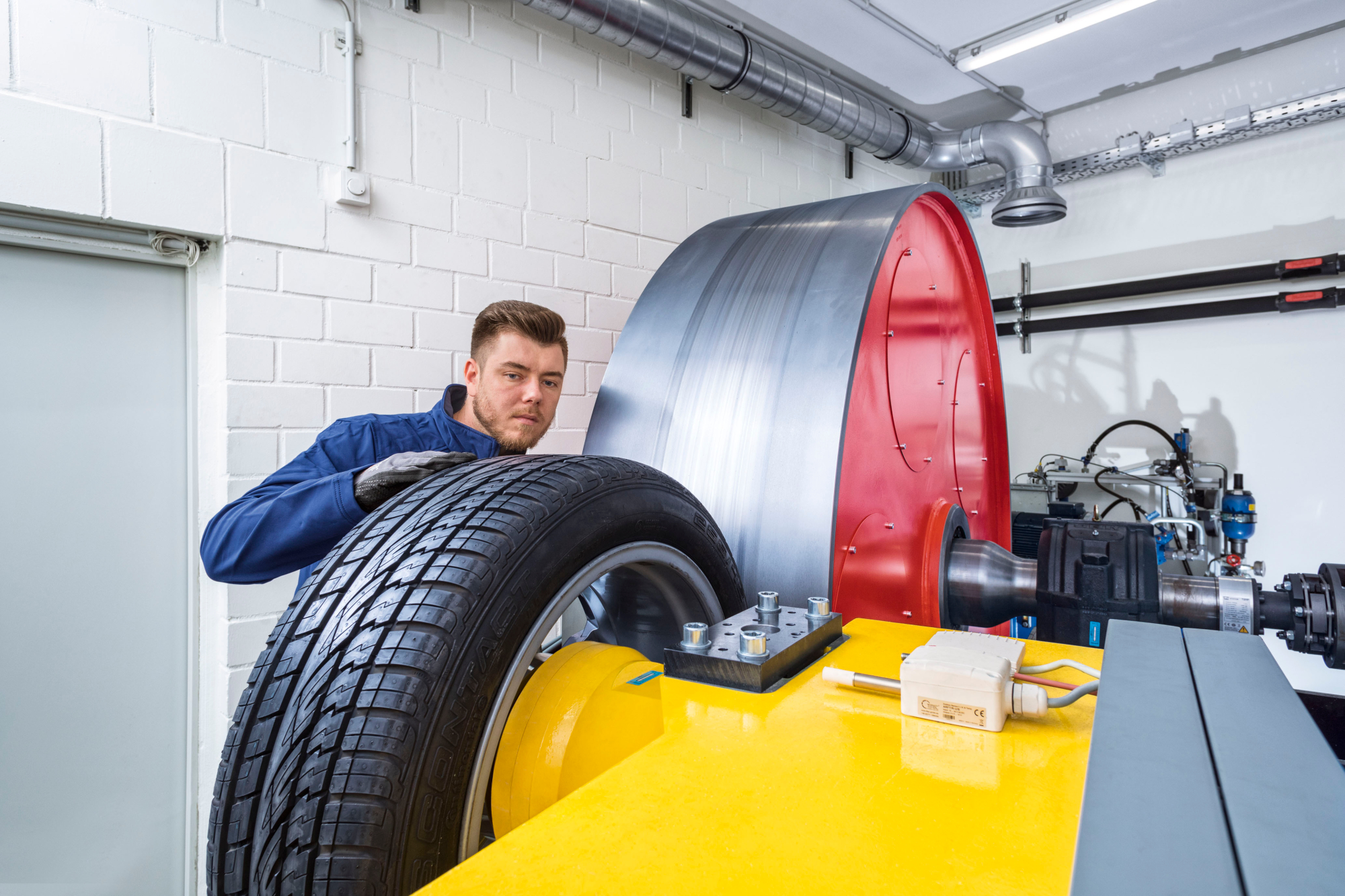
Holistic Testing
IAV offers comprehensive testing for chassis systems, starting from the early development phase. Our virtual testing capabilities help avoid costly detours at the beginning of the development process. As development progresses, we provide testing for chassis components such as brakes and tires, XiL testing of control units, sensors, and actuators, as well as material properties, culminating in prototype testing on the vehicle. Our brake and tire test benches assist in meeting ambitious CO2, wear, and particle emissions targets.
Smart Test Bench Coupling
Our highly dynamic brake test benches can be coupled with our HiL test benches, allowing brake control functions to be tested alongside real brake systems without needing a prototype vehicle. This enables the definition of matching material properties at an early development stage and evaluation of their effects on wear and particle emissions.
Road to Rig & Road to Sim
We help reduce outdoor vehicle testing to enhance reproducibility and save costs. This includes brake endurance testing on the chassis dynamometer, incorporating airflow simulation to mimic real ambient cooling conditions and lateral forces from cornering maneuvers. We develop solutions to advance testing into the virtual realm, utilizing physical and data-driven models combined with real physical testing on the test bench.
Our Chassis Test Capabilities
„We drive innovation in chassis development, offering unparalleled expertise from concept to completion, ensuring every journey is safe, comfortable, and exhilarating”
Dr. Toni Feißel